Vi former fremtidens
havbruk
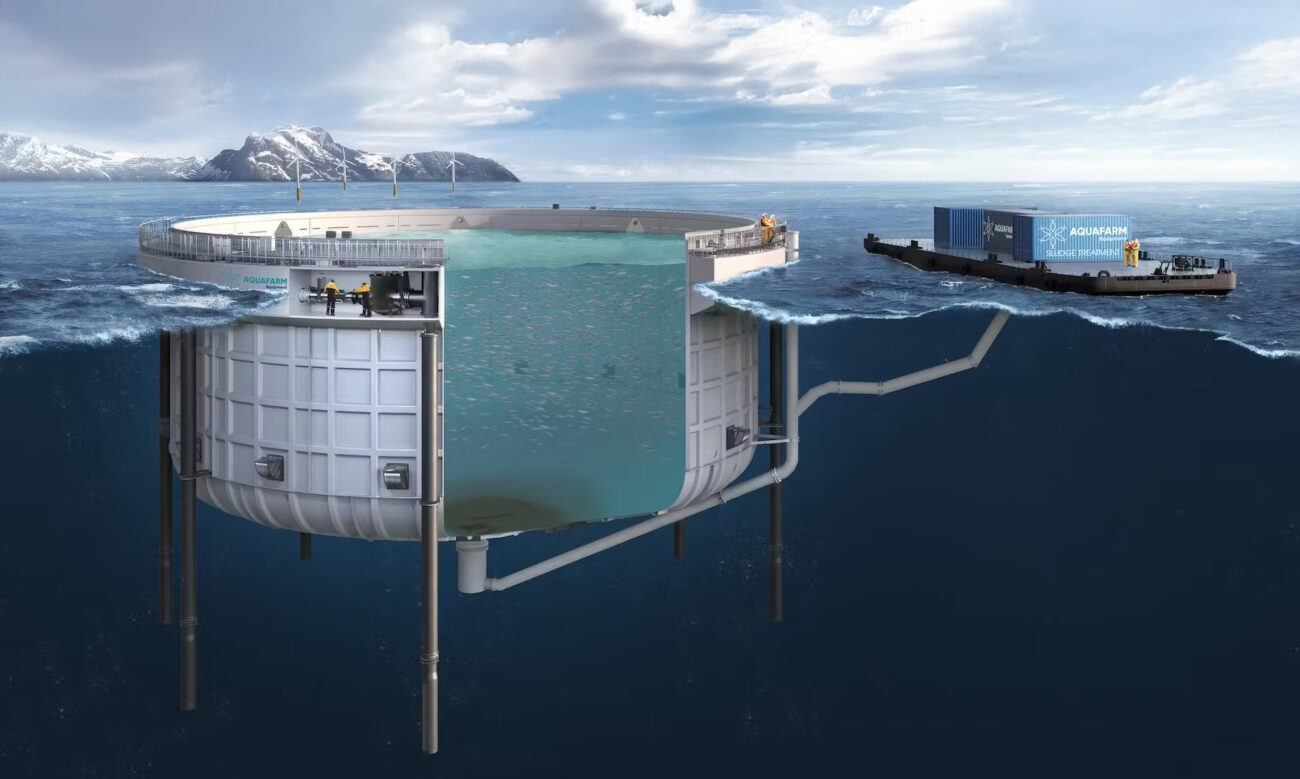
En viktig industri
Havbruk er nøkkelen for å sikre den globale matforsyningen. Bransjen vår har kommet langt med tanke på bærekraft, men vi har fortsatt en lang vei å gå.
En ny tilnærming
Vi bryter med konvensjonell visdom i bransjen og setter oss et nytt, dristig mål. Vår visjon er fiskeoppdrett uten fotavtrykk.
Innovasjoner i bransjen
Innovasjoner i bransjen springer ut av behovet for å kutte kostnader, tilpasse seg reguleringer og øke fortjenesten.
En viktig industri
Havbruk er nøkkelen til å sikre den globale matforsyningen. Bransjen vår har kommet langt i retning av å bli mer bærekraftig, men vi har fortsatt en lang vei å gå.
En ny tankegang …
Å prioritere fiskevelferd løser mange problemer. Fisk som trives, reduserer forurensning, minimerer matsvinn og øker fortjenesten. Vår unike tilnærming starter med å skape sunnere habitater, noe som fører til flere fordeler.
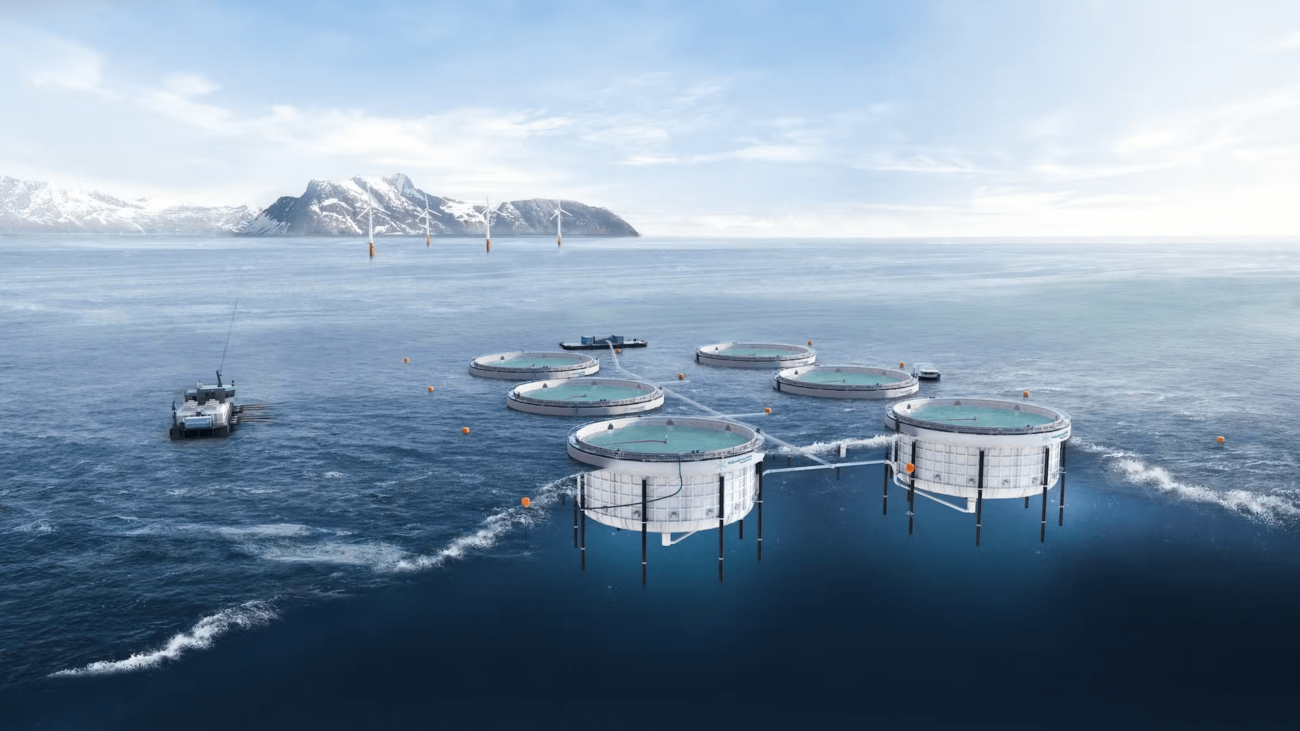
100 % rømningssikker
Oppsamling av slam
Full økosystemkontroll
Ingen opphopning av lakselus